Fisher
Body - Home
Fisher Body Craftsmanship Goes to War
Fisher Body - Craftsmanship
Fisher Body - Aircraft
Fisher Body - Aircraft
Instruments
Fisher Body - Guns
Fisher Body - Tanks
Fisher Body - Miscellaneous
The Plants
Fisher Body WWII Plant Database
Cleveland Plant #1, OH Plant
Cleveland Plant #2, OH Plant
Detroit Aircraft Unit,
Detroit, MI
Detroit Die and Machine Plant
Fleetwood, Detroit, MI Plant
Flint Plant #1, MI Plant
Grand Blanc, MI Tank Arsenal
Grand Rapids, MI Plant
Lansing, MI Plant
Memphis, TN Plant
Ternstedt Manufacturing Division,
Detroit, MI
Grand Blanc Tank Arsenal Built Tanks and Tank Destroyers
Grand Blanc
built M4A2 Sherman Tank Photos
Grand Blanc
Built M4A3 Tank Photos
Grand
Blanc M10 Tank Destroyer Photos
The Fisher Body Flint, MI Plant #1 in World War Two
A Surviving Fisher
Body Plant - Administration Building only
1926-1987
This page updated 11-7-2019.
Author's note: Seventy-three
years after the end of World War Two, and eighty-one years after the end
of the 1936-37 sit-down strike at Fisher Body #1, I looked back at
events during the tumultuous years from 1936 to 1945; and have reviewed
what happened at the plant with a new and different prospective.
To a large extent, the Flint Fisher Body #1's (Flint #1) contribution to the winning of
World War Two has been overshadowed by the more well known Grand Blanc
Tank Arsenal, 4.5 miles south of Fisher Body #1. My investigation
shows that the two plants worked very closely together to produce the
19,034 armored fighting vehicles that were produced that came off the
assembly lines of the Fisher Body Grand Blanc Tank Arsenal.
The American Automobile
Industry's Unrecognized Sherman Tank Plant - Fisher Body Flint Plant #1:
In April1942, M4A2(75)VVSS Serial Number
2305 and Registration Number 3014311 came off the improvised assembly
line at Flint Fisher Body Plant #1. Serial number 2305 then made
the 4.5-mile trip down Saginaw Street to the Grand Blanc Tank Arsenal, still under construction, to use its newly
built test track.
Flint Fisher Body #1 built the first twenty
Sherman tanks produced by the Fisher Body Division of General Motors.
This fact has been overlooked. When recognized by Sherman tank
historians, the twenty M4A2s are included in Grand Blanc's production
numbers. I disagree with this. Flint #1 was its own entity
and needs to be recognized as a tank plant in its own right.
The following quote is from page 24 of
Fisher Body's war history, "Fisher Body Craftsmanship Goes to War."
"Actual production was started in January 1942 in a converted section of
Fisher Body's large plant in Flint, Michigan, sixteen days before the
last automobile body was completed. The first M-4 came off the
line under its power just 47 days after work was started, and a new tank
was born." The article goes on to state that the Grand Blanc Tank
Arsenal was being constructed, and that final assembly of the Sherman
tanks moved to that location when it was completed.
That brings up the question of how many
M4A2s did Flint #1 build, and when did production start at Grand Blanc?
Information from page 359 of "The Sherman - Design and Development"
(Better known as "Son of Sherman - Volume 1.") by Patrick Stansell and
Kurt Laughlin provides clues. It shows Grand Blanc building four
M4A2s in April, and sixteen in May 1942. The authors state on page
18 that Grand Blanc started production in July 1942. This is
incorrect. They probably meant to say June. Flint #1 was not
equipped to turn out 177 Sherman tanks in one month. They note
that tanks had been previously built at a Fisher Body plant in Flint,
which would be Flint #1. The authors identify Fisher Body as a subsidiary of General Motors.
This is also incorrect. It was a division of GM. At the time of
World War Two, it was the largest division within GM, even larger than
Chevrolet. How Grand
Blanc was able to produce so many tanks its first month in production
will be addressed later on this page. The takeaway at this point
is that the first 20 Sherman tanks built by Fisher Body Division were
built in Flint #1.
Flint Fisher Body Plant #1 Administration Building:
This is the most historically significant of
all of the Fisher Body Plants but all of the auto plants, if not all US
auto plants, because it was here during a sit-down the 1936-37 strike
which caused General Motors
to recognize the UAW. The plant, with the exception of this
historic building, was torn down in 1988.
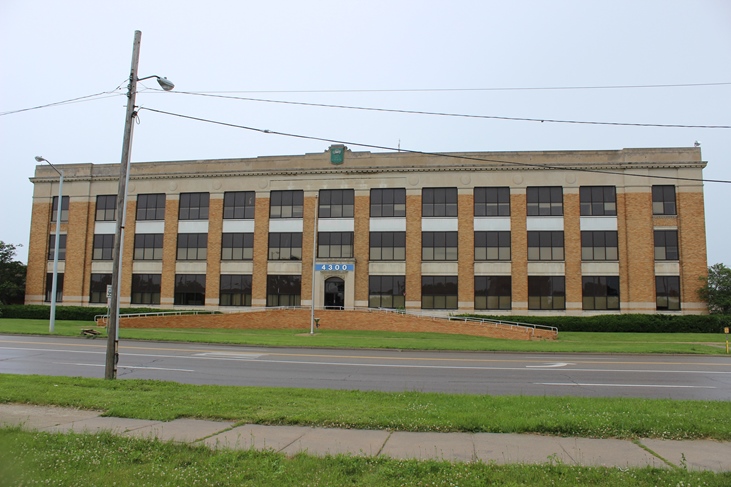
This is the former administration
building of the Flint Fisher Body #1. This building is the site of
important American history. The 1936-37 sit-down strike happened
in front and in the factory buildings that formally stood on either side
of it. With the settlement of the strike, the recognition of the UAW by General Motors, and
eventually the entire U.S. auto industry, it became easier for the
American auto workers to join the Middle Class. With good wages and company furnished
health benefits, auto workers became the backbone of the American Middle
Class. With the closing of the plant and others like it, not only
in the American auto industry, but other manufacturing industries as
well, the American Middle Class went into decline, as factory workers lost their jobs to cheap labor in third
world countries.
Built in the 1920s, this building was
originally the headquarters for Durant Motors. General Motors
bought this building and the former Durant Motors automotive assembly
plant in 1926 for $4
million. As part of Fisher Body, it
produced bodies for the Buick plant on the north side of Flint. Author's photo.
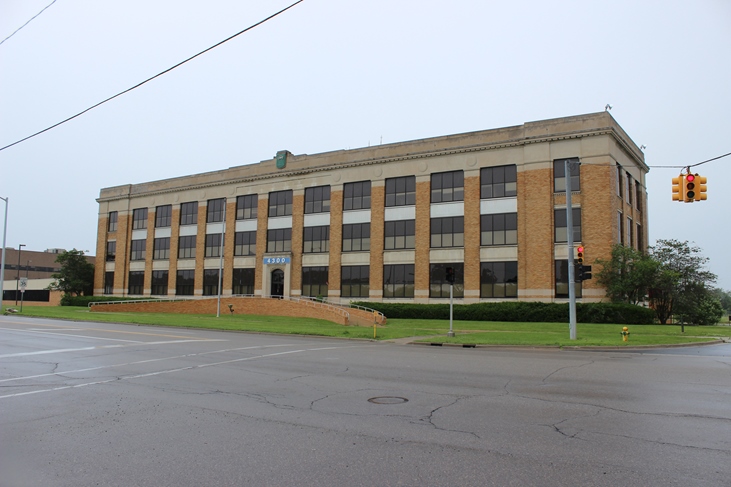
Author's photo.
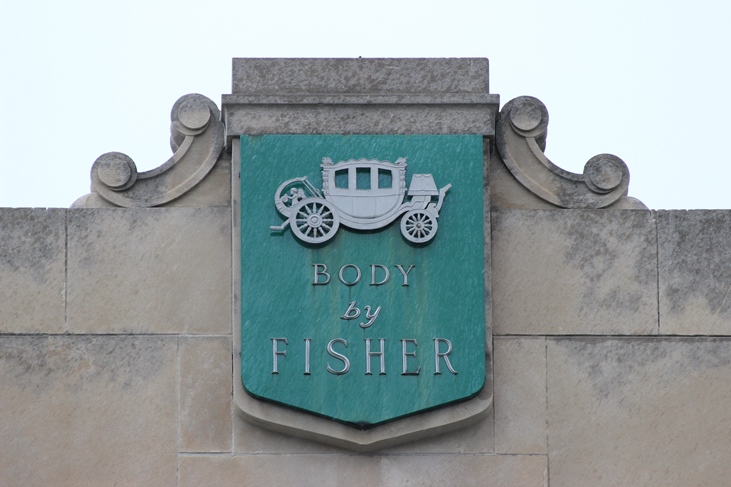
To my knowledge, this symbol and slogan of
the once powerful and now defunct Fisher Body
Division of General Motors can only be seen at the top of the former
administration building of Fisher Body #1. It is the only one
left! Author's photo.
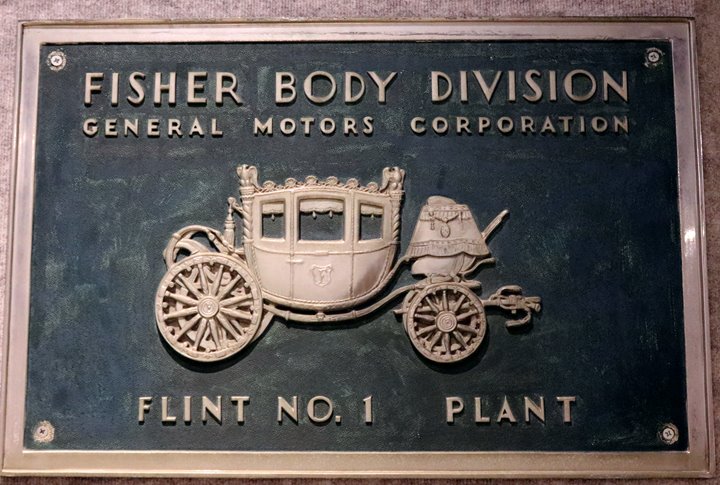
This plaque from Fisher Body Flint No. 1 is
on display at the Sloan Museum in Flint, MI. Author's photo.
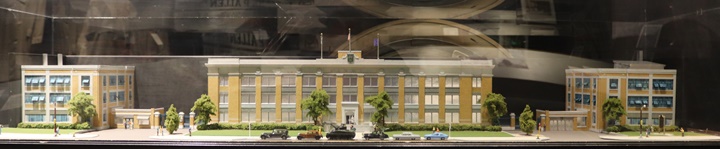
There is a model of the administration
building on display at the Sloan Museum. Author's photo.
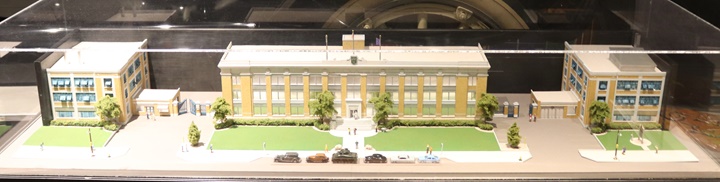
Author's photo.
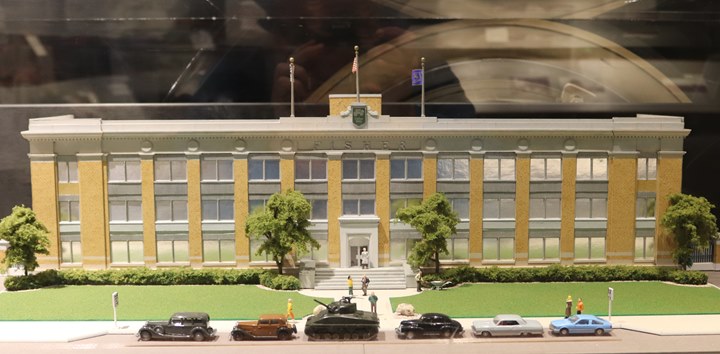
Out in front of the model building are some
of the products that plant built from 1926 to 1988. With the
exception of the model of the M4 Sherman tank, the rest of the vehicles
are Buicks. This plant made the bodies for the Buicks produced on
the north side of Flint. Author's photo.
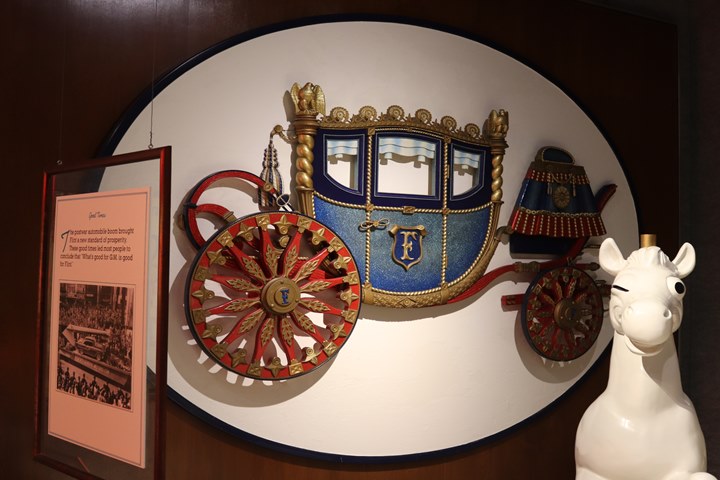
The Fisher Body Coach emblem is also located at the Sloan Museum among
other displays. Author's photo.
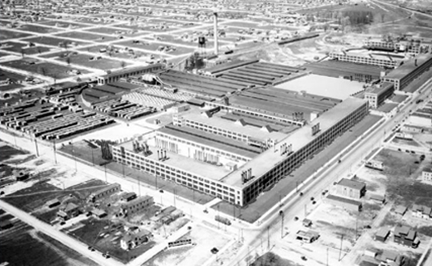
An aerial photo of Fisher Body #1 looking north-west. The
administration building can be seen in the upper right of the photo.
The entire complex was bounded by Hemphill Road on the south, Atherton Street on the north,
and Saginaw Street to the east. Note that the streets have been laid out
to the west of the plant; but only a few houses dot the area. Today,
I-475 runs through where those houses were. The plant was
originally built in the 1920s as part of the Durant Motors and was the
headquarters for the company. Inside this plant in early 1942,
twenty M4A2 Sherman tanks were built.
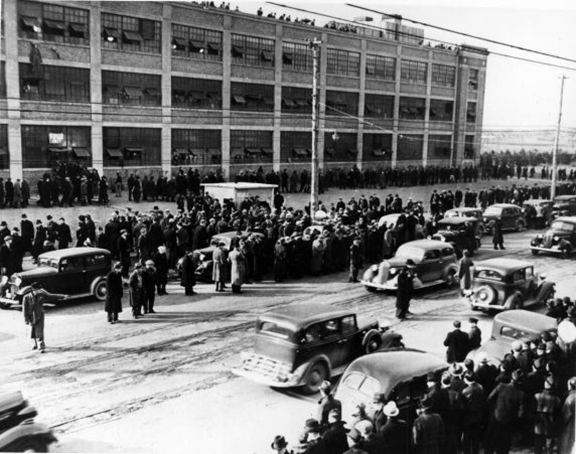
A period photo taken during the sit-down
strike. Supporters of the strike are outside Fisher Body Plant #1 along Saginaw Street.
The strikers can be seen atop the plant and in the windows.
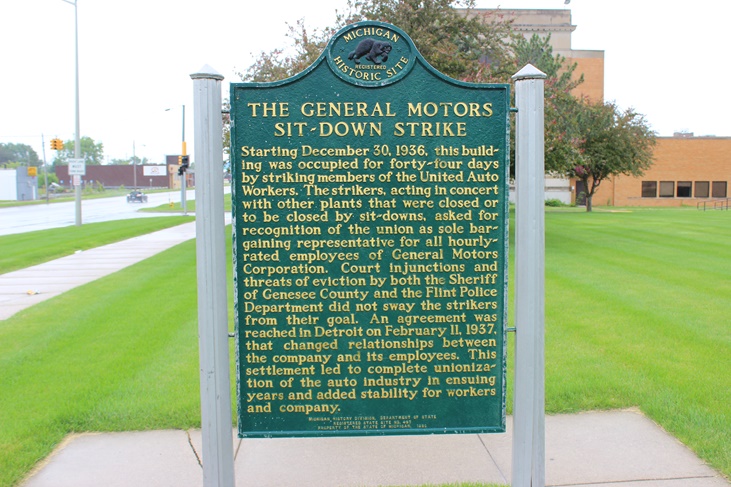
This historical marker, explaining the events which took place
here in late 1936 and early 1937, stands just to the north of the
administration building. The Administration building can just barely
be seen behind the trees. Author's photo.

A historic location in US auto industry-union relations that has now
been forgotten over time. Author's photo.
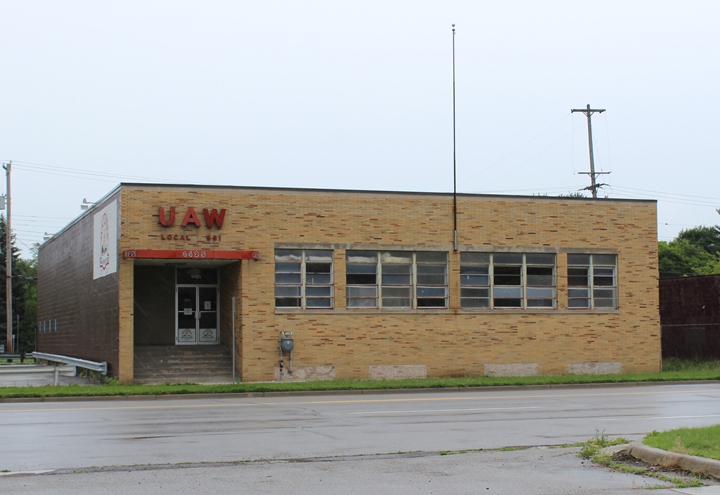
The UAW Local 481 union hall also still
stands across the street from the Administration
building. Now forlorn and ignored, it too has been relegated to
the scrap heap of forgotten history. Author's photo.

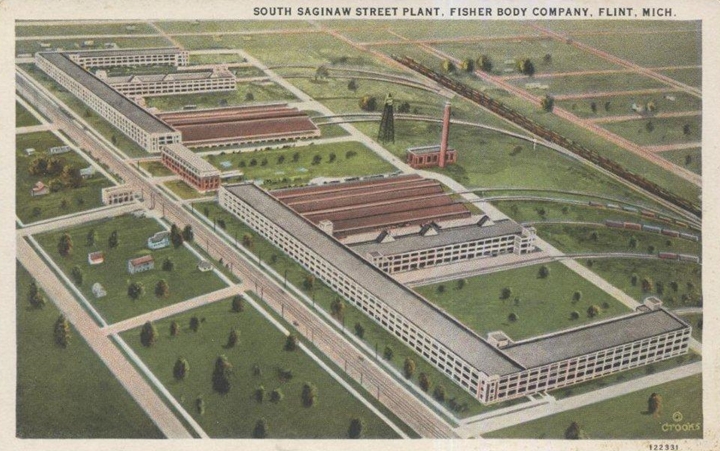
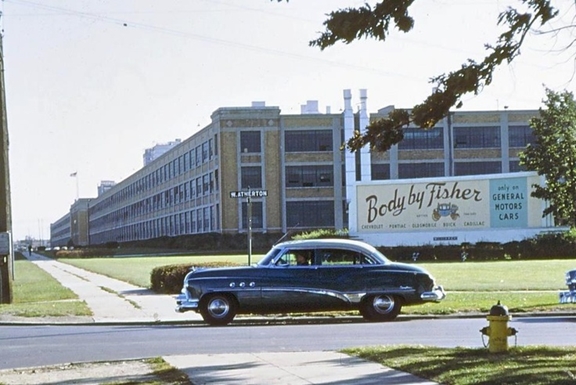
This nostalgic 1950s photo shows the north end of
Flint Fisher Body #1 looking south down Saginaw Street.
From the visible shadows, it is late afternoon and the first shift is going home.
The worker leaving the plant is driving what he made, a Buick. The
body was made in the plant behind him, with the final assembly of the
vehicle done four miles to the north at the Buick plant.
World War Two:
Fisher Body Flint Plant #1 was awarded the
Army-Navy "E" Award five times during World War Two.
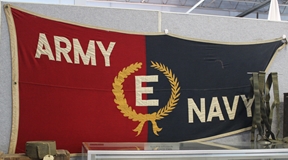
Fisher Body Flint Plant #1 was awarded the Army-Navy "E" Award on January 15,1943.
The plant was awarded its first star on September 22,1943, for the timely production of M4 Sherman tank and M10 Wolverine tank
destroyer parts.
It received its second star on July 30,1944, for the timely delivery of
22 development models.
The third star was awarded March 5,1945.
The fourth star was awarded May 17,1945.
Fisher Body Flint #1 World War Two Products: M4, M10, M26, M36,
M18 Tank Parts and Tank pilot models and parts. M4, M10
Experimental Models. Tank Tools and fixtures. 120mm and 155mm Gun Parts, 5-inch Naval Gun parts, B-29 and XP-75 Aircraft
fixtures.
Author's note on the importance of Flint
Fisher Body #1 in World War Two: The World War Two history of
Flint Fisher Body is intertwined and overshadowed by the Fisher Body
Grand Blanc Tank Arsenal 4.5 miles south on Saginaw Street. The
19,014 tanks, tank destroyers, and prime movers it built are better
documented than the work Flint #1 did to make the building of those
armored fighting vehicles possible. What was lost after the war
was the knowledge that Flint #1 was an extension of Grand Blanc, and
vice versa. Grand Blanc was a high output plant where the prime
goal was to assemble tanks and tank destroyers as quickly as possible
for the U.S. Army. Flint #1 developed the tooling and fixtures,
and then tested them before shipping them to Grand Blanc where they were
installed and brought up to line speed with a minimum of lost time. Many of the prototypes
for the changes and new tanks and tank destroyers produced at Grand
Blanc were built and tested at Flint #1. High volume production of
any product involves making tooling and fixtures ahead of time.
This is what Flint #1 did. It was Grand Blanc's main tool room and
engineering center.
M4 Series Sherman tank:
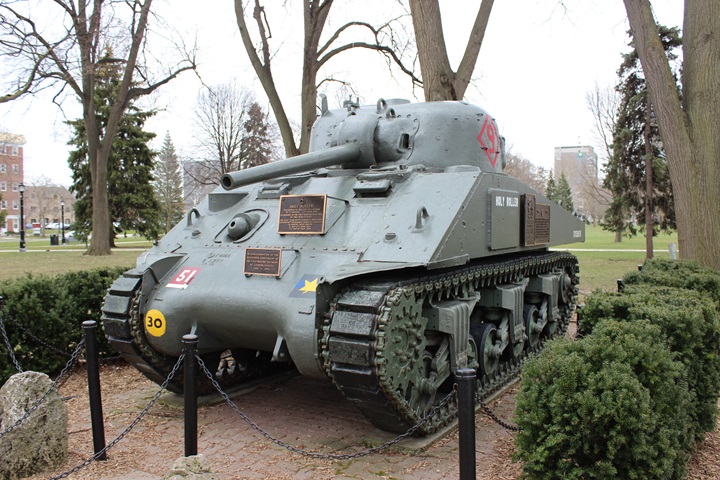
The twenty M4A2 small hatch tanks built by
Flint #1 would have looked very much like this one built at Grand Blanc
in September 1942. This is the oldest Fisher Body built M4A2 in North
America. Author's photo.
In June 1942 the Grand Blanc Tank Arsenal
produced 177 M4A2 Sherman tanks. It could never have produced that
many in its first month of production without the lessons learned from the first 20 produced at Fisher #1
in April and May 1942.
There were many changes to the various models
of the 11,338 M4 Sherman tanks produced by the Grand Blanc tank arsenal
during WWII. Sherman production started with the M4A2 small hatch
with dry storage for the 75mm main gun ammunition. Later, an
improved version of the M4A2 had larger hatches for the driver and
assistant drivers, which totally changed the configuration of the front
glacis and how it mounted to the side armor plates. Flint #1
redesigned and made tooling and weld fixtures, and then tested them on
prototype parts
before the tooling and fixtures were shipped to Grand Blanc for
installation. Flint #1 also did the same thing for them when the
M4A2 was modified internally for wet 75mm ammunition storage. When
the M4A2 was converted to a 76mm main gun, Flint #1 developed
tooling for machining the newer, larger turret.
In February 1944 Grand Blanc started
production of the large hatch M4A3(75). While similar to the
M4A2(75) it was already producing, the M4A3 had a different engine.
Before production started, Flint #1 worked on reconfiguring the engine
bay from having twin six-cylinder diesel engines to a single V-8
gasoline engine. All of the internal connections to the main tank
had to be redone before the tank could be released for high speed
production.
Fisher Body #1 would have done the prototyping
and built many of the tools and weldments for the following versions of
the Sherman tanks built by Grand Blanc during the war.
When production stopped in May 1945 on M4
series tanks at Grand Blanc, 1,100
workers were laid off at Flint Fisher Body Plant #1. These
employees would have been making parts for the Sherman tank built at
Grand Blanc.
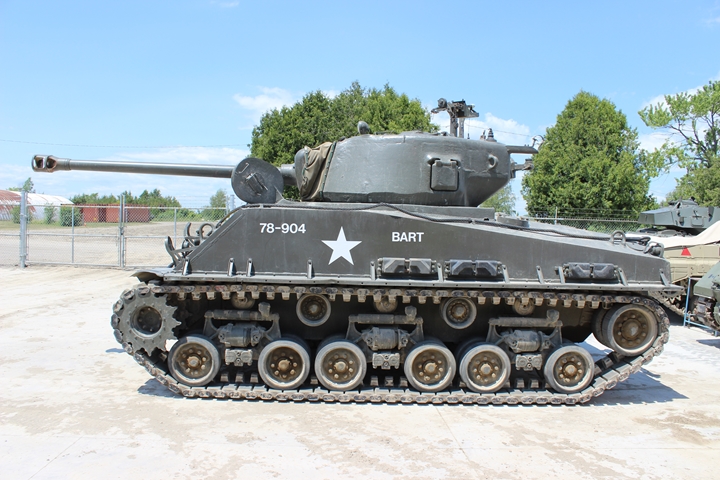
This is the M4A2 large hatch with 76mm main
gun and HVSS suspension. Author's photo.
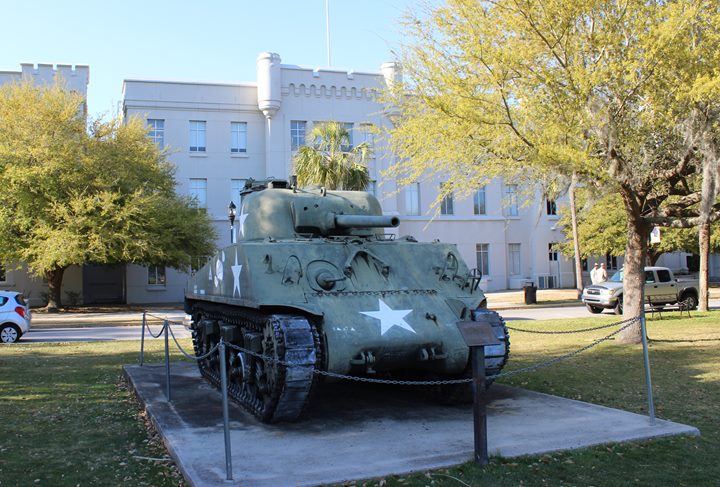
Grand Blanc originally started out
building the M4A3 version of the Sherman with large hatches, VVSS
suspension, and a 75mm main gun. Author's photo.
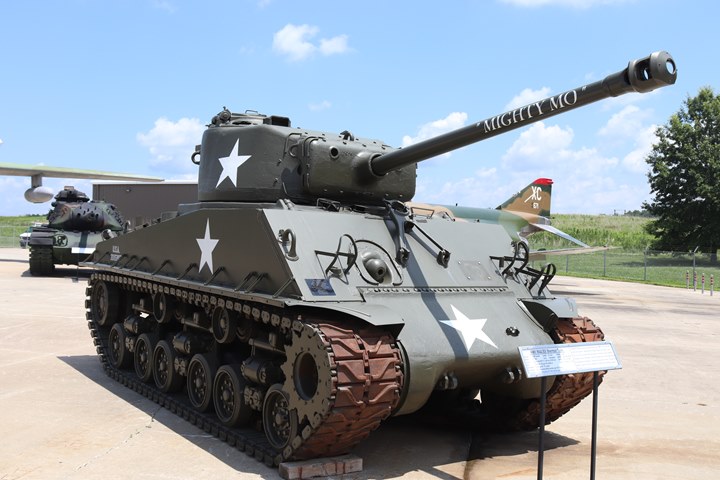
The final version of the Grand Blanc built
M4A3 had a 76mm main gun and a HVSS suspension. Author's photo.
M10 Wolverine tank destroyer development:
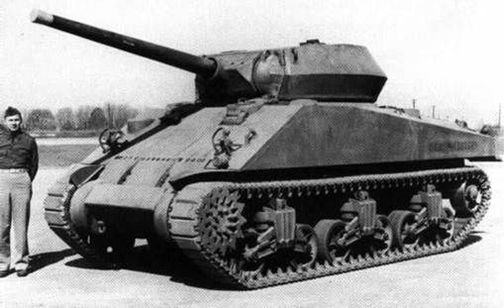
This is the T35 prototype for what became the
M10 tank destroyer. Note that the hull is the same as a M4A2
direct vision tank. The date of the photo is April 23, 1942, which
was before Grand Blanc went into production. Therefore, this
prototype was built in its entirety on the same assembly line that built
the first 20 M4A2 Sherman tanks. Flint #1 fabricated the rounded
turret for the prototype.
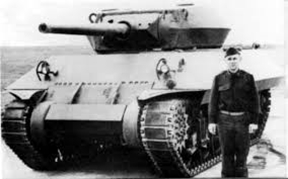
This is the second tank destroyer prototype,
T35E1 on May 4, 1942. Once again this was before Grand Blanc was
open. The hull design is now closer to the final version of the
M10. Engineers at Flint #1 had to modify welding methods to
accommodate the thinner armor plate used on the M10s, and then build the
appropriate fixtures for high volume welding at Grand Blanc.
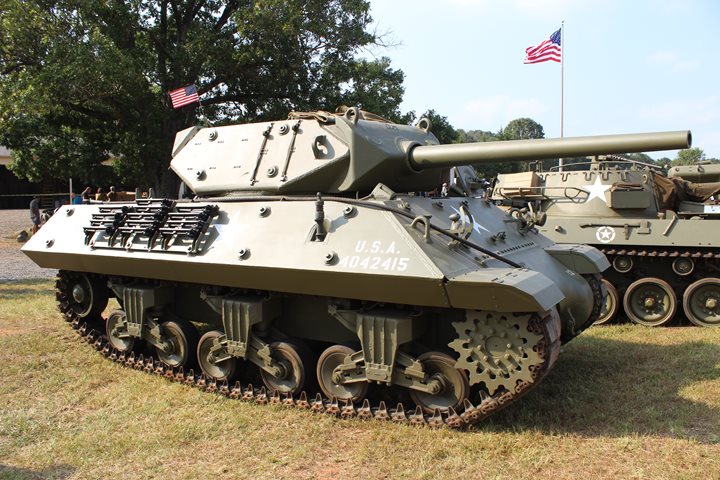
This is the final product with the flat-sided turret. This Fisher
Body Grand Blanc M10 was built in April 1943. Author's photo.
M26 Pershing tank development: In late 1944 production of the M26 Perishing
heavy tank began at Grand Blanc. For several years there had been
much development and several different prototypes built before the
design release of the M26 Pershing. Fisher Body Flint #1 engineers
worked with U.S. Army Ordnance on these various prototypes; The plant built the
fixtures and tooling to produce two T20 tanks in May 1943, 40 T25E1
tanks from February to May 1944, and ten 26E1 heavy tanks also from
February to May 1944. In the case of the two T20s, they may very
well have been assembled at Flint #1 rather than interfere with the high
production Grand Blanc lines.
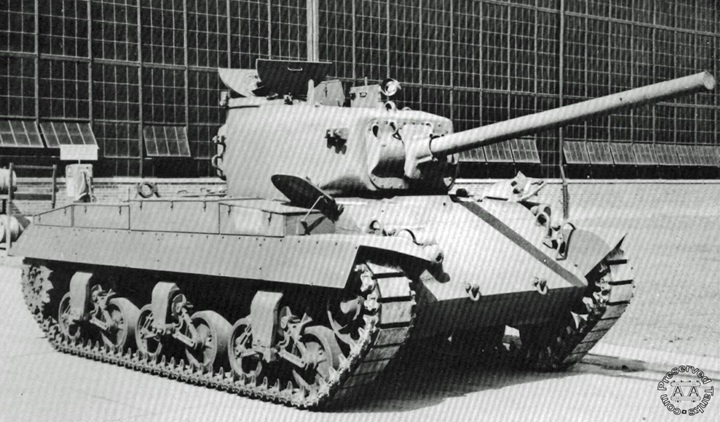
Fisher Body was given the contract to
produce two T20 experimental medium tanks. This is the first one
with VVSS suspension that was completed in May 1943. No doubt
Fisher Body Plant #1 was largely involved in making this vehicle.
This was USA registration number 30103302.
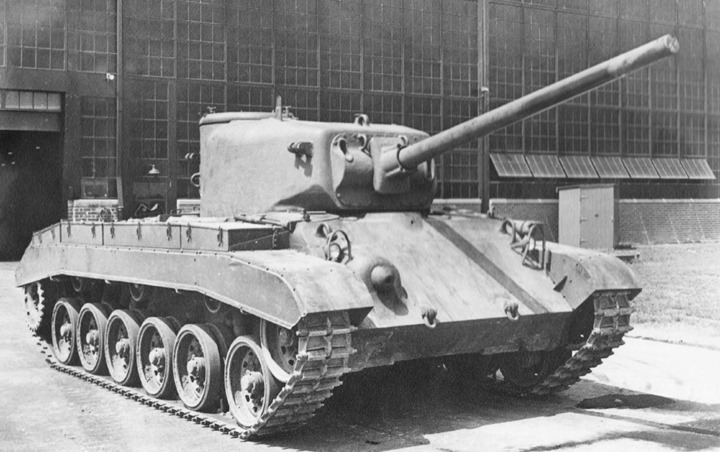
The second prototype was designated T20E3
and had a torsion bar suspension. Registration number 30104303 was
completed in July 1943.
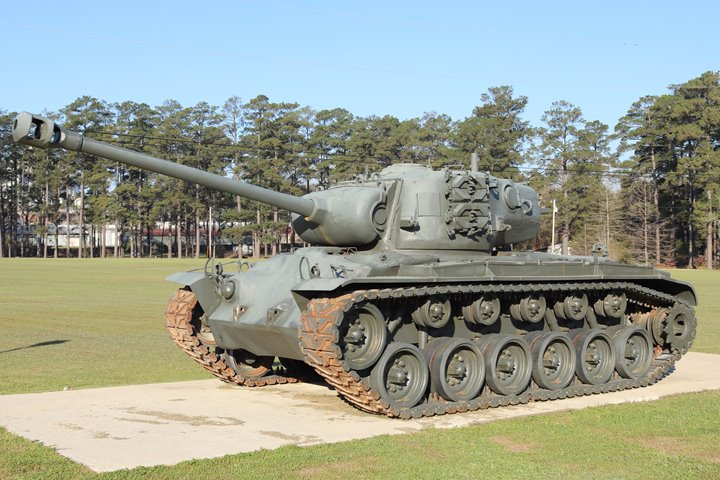
The final product was 1,729 Grand Blanc
built M26 Pershing heavy tanks. This one is serial number 567.
Work stopped on the M26 at Flint #1 on October 5, 1945. Author's photo.
Fisher Body Flint # 1 / Grand Blanc
shared World War Two Products: The products listed below are in
listed in "Fisher Body Craftsmanship Goes to War" tank section of
the book. It does not specifically say whether Grand Blanc or
Fisher Body Plant #1 did the work. Probably Grand Blanc did a lot
of the large weldments as it was set up for that. But Fisher Body
#1 did all of the development work, and probably did many of the small
weldments and subassemblies.
Tank and Tank Destroyer Components -
Weld fixtures and tooling for
(2,245) M18 turrets, (1,511) M18 hulls, the conversion of (600) older M18s
into M39 prime movers, and the new construction of (40) new M39s.
Fixtures for (487) M36 tank destroyers
M18 Turrets and Hulls: Buick was
the prime contractor for the M18 Hellcat tank destroyer. However,
because it was aware that Fisher Body #1 on the south side of Flint and
the Grand Blanc Tank Plant were more experienced in the fabrication of
armored plate, it asked Fisher Body to build the tooling, weldments and
many of the turrets and hulls. There was a total of 2,507 Hellcats
made. Fisher Body built 90% of the turrets, and 60% of the hulls.
Due to the fact that the armor plate was thinner on the M18 than the
M10, (Which wasn't all that thick to begin with!) engineers at Fisher
Body Flint #1 had to develop different methods of welding to prevent distortion. Heavy duty weldments had to be made to
combat the problem.
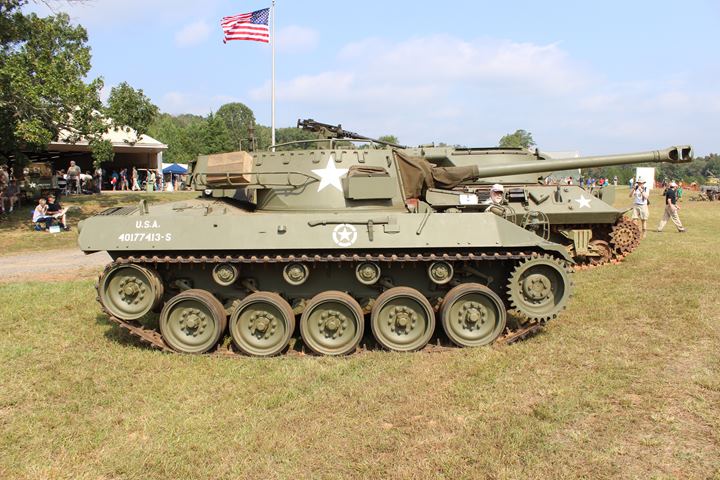
The M18 Hellcat with turret and hull welded by Fisher Body.
Author's photo.
M39 Prime Mover: Buick was also
the prime contractor of this vehicle, but Fisher Body Flint #1 and Grand
Blanc did all of the work. Fisher Body converted 600 previously
used M18s
to the M39 Prime Mover. Fisher Plant #1 did the
design changes and built the necessary fixtures. Another 40 brand
new M39s were built by Fisher Body.
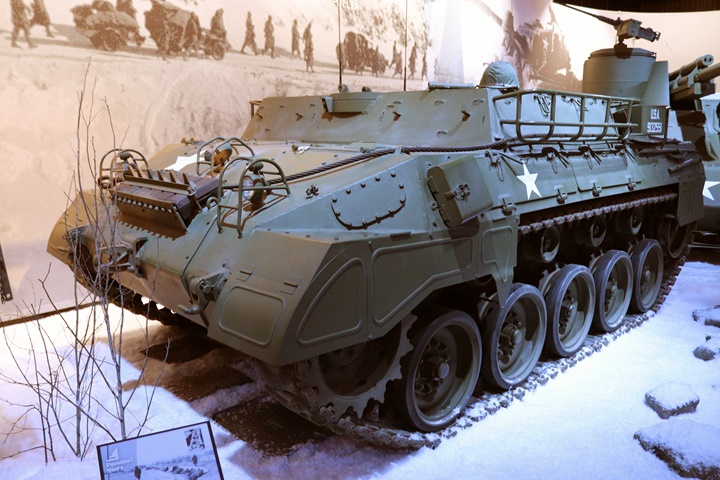
This is one of only twelve M39s that still
exist of the 640 that were originally built or converted from the M18
Hellcat. Mostly likely the 600 conversions were done at Flint #1
to not slow down the production of the M26 Pershing heavy tank at Grand
Blanc. An assembly line could have been set up to remove the
turret and gut the interior. The armored shield that went around
the crew area would need to then be welded on, and the the new interior
installed. The new 40 M39s could have been built in either plant
but most likely this would have been done at Grand Blanc as the hull
needed to be welded. After that they could have been sent to Flint
#1 for the interior install. Author's photo added 11-7-2019.
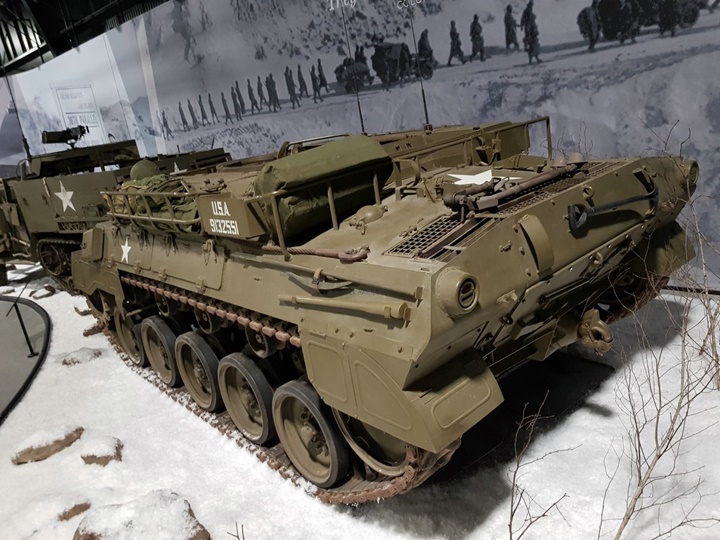
Image courtesy of Pierre-Olivier Baun added
11-7-2019.
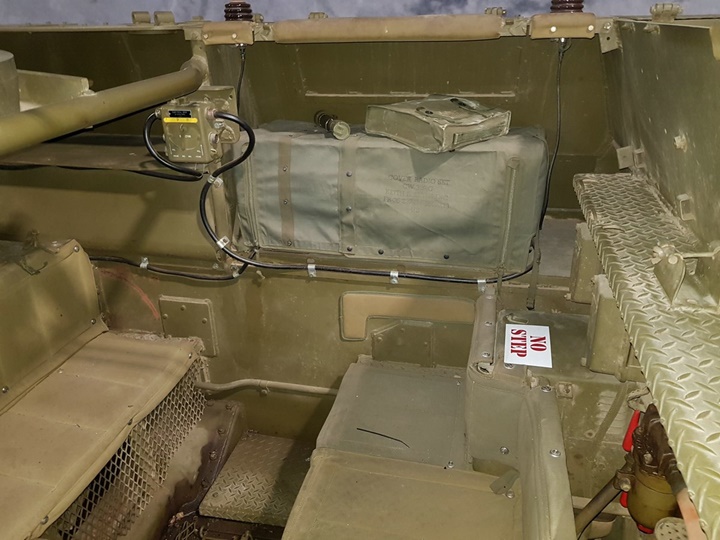
Image courtesy of Pierre-Olivier Baun added 11-7-2019.
M36 Turrets and Conversion of M4A3 M10, and
M10A1 Hulls for 90mm ammunition: In November 1943 Fisher Body
was authorized to build 300 M10A1 Wolverines without turrets.
These would be converted to the new M36 tank destroyer with a 90mm main
gun. The M10A1 hull interior had to be extensively
redesigned by Flint #1 engineers to accommodate the larger 90mm
ammunition. New weld fixtures and prototypes then had to be built by Fisher #1 to test to see if they fit properly.
Fisher Plant #1 also designed a brand new
hydraulically controlled turret for the larger 90mm main gun. A turret
basket was added and an improvement in the electrical wiring.
Enough fixturing had to be built not only for the M36s coming down the line
at Fisher Body Grand Blanc, but also for another 719 turrets being
supplied to other manufacturers converting the M10A1 into the M36.
The same turret was applied to converting 187
M4A3 tanks taken off the line to make the M36B1. The M4A3 had to
have the interior of the hull redesigned for the 90mm ammunition of the
larger gun. Fisher Body #1 did the redesign of the interior, made
the ammunition trays, and delivered them to the Grand Blanc Tank Arsenal
so that the first prototype was completed in only five days.
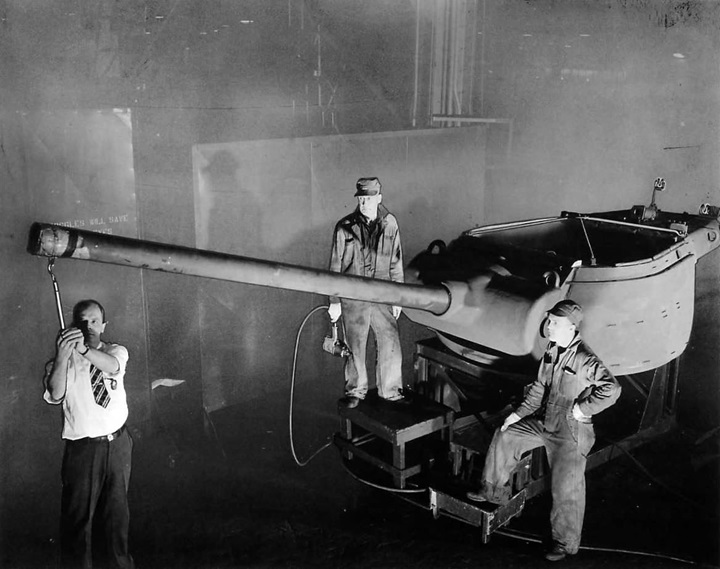
A M36 turret under construction at the Grand
Blanc Tank Arsenal. The design was done by Flint Fisher #1.
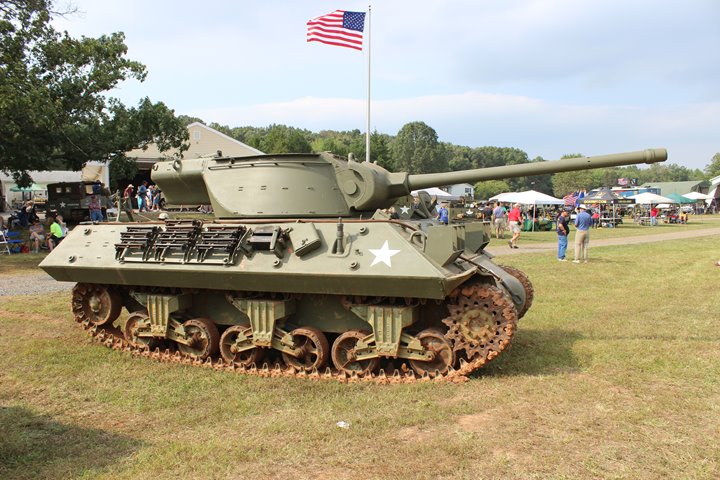
This M36 is seen on display at the Virginia Museum of Military Vehicles in
Nokesville, VA. Author's photo.
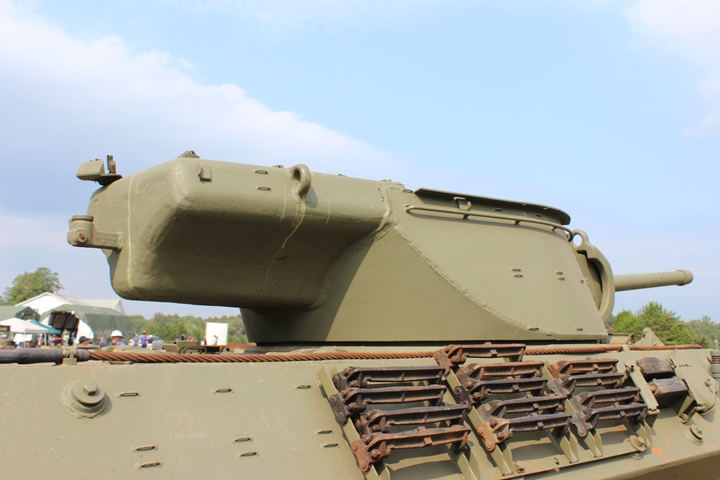
The Flint Fisher Body #1 designed M36 turret.
Author's photo.
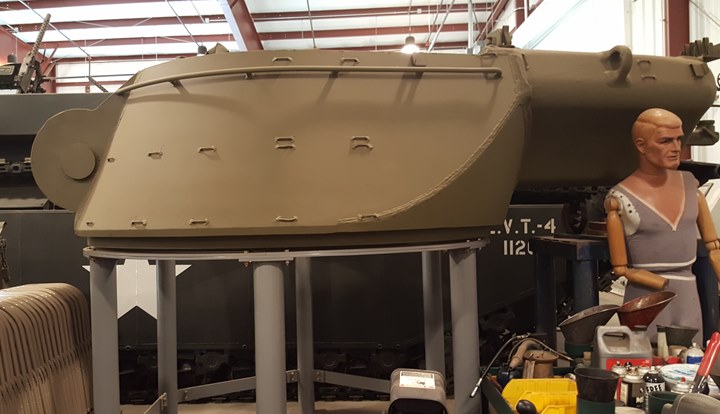
This M36 turret is on display at the Museum
of American Armor on Long Island, NY. Photo courtesy of Rudy Lev.
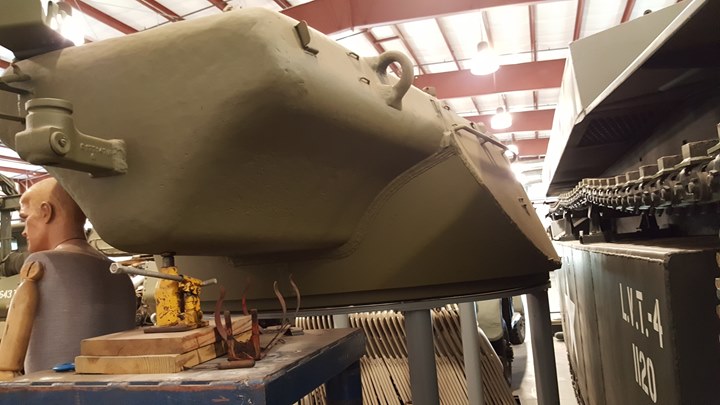
Photo courtesy of Rudy Lev.
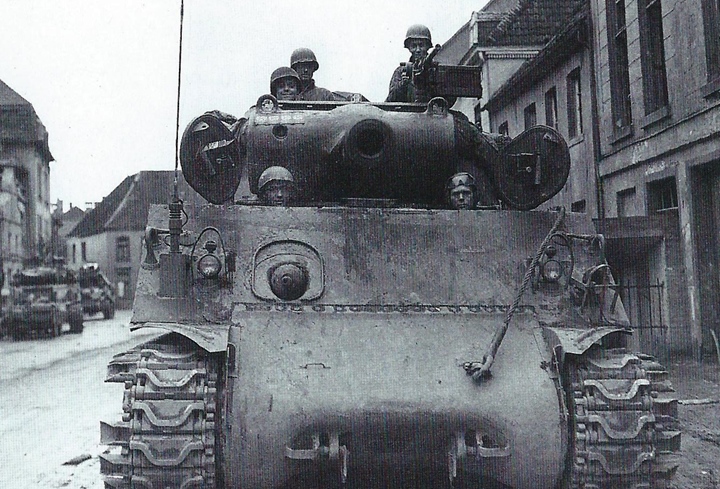
This is a rare photo of one of the 187
Fisher Body built M36B1 Jackson tank destroyers in the European combat
zone. Note on the Fisher Body #1 designed turret are four victory markings indicating this
M36B1 has destroyed two German Tiger tanks and two Panzer IVs. The
new 90mm main gun was doing its job! This Grand Blanc built unit
is serving here with the 654th Tank Destroyer Battalion.
5-Inch, 38 Caliber Naval Gun parts:
The Fisher Body Die and Machine Plant in Detroit, MI, and the Grand
Rapids, MI Fisher Body plants produced 6,342 five-inch breech housing
for five-inch naval guns during WWII. Flint #1 provided parts to
these two plants for the five-inch guns.
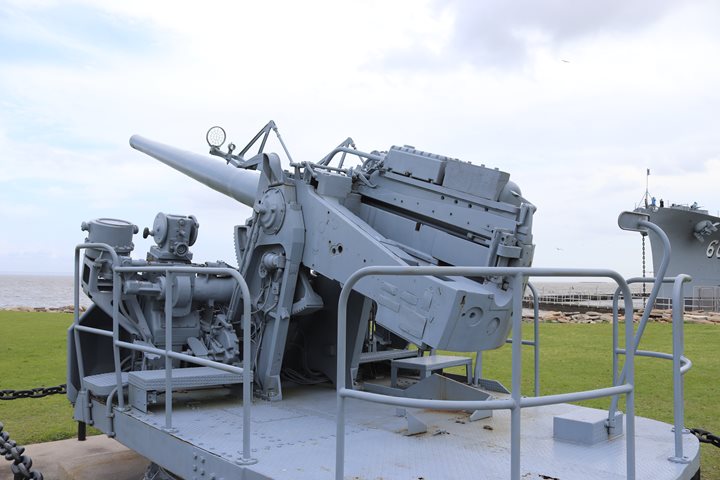
Fisher Body Flint #1 produced parts for five-inch, 38 caliber guns like this one. The breech weighed 2,932 pounds and was the heart of the gun mechanism
that contained 218 pieces. Author's photo.
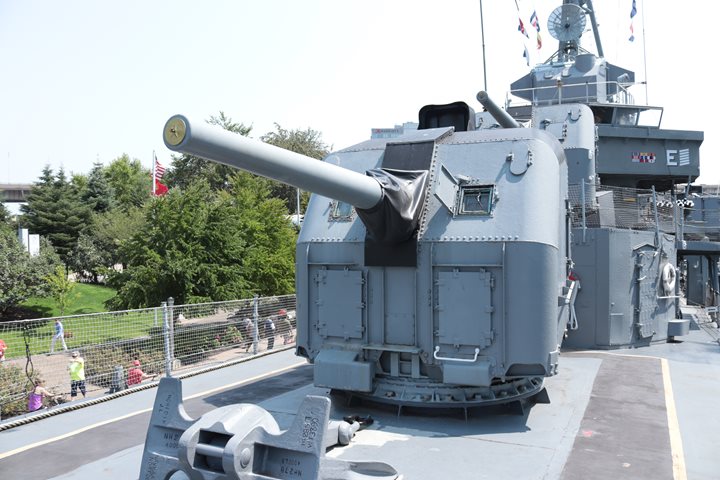
The
five-inch gun encased in an armored turret is probably more recognizable
as the main weapons on American destroyers during World War Two.
This one can be seen at the USS Sullivans at the Buffalo and Erie County
Naval and Military Park in Buffalo, NY. Author's photo.
120mm M1 Anti-Aircraft
Gun parts: Fisher Body Grand
Rapids was the sole producer of 550 120mm M1 Anti-Aircraft guns which
entered service with the US Army in the Philippines in 1945. Flint
Fisher Body #1 made parts for this weapon.
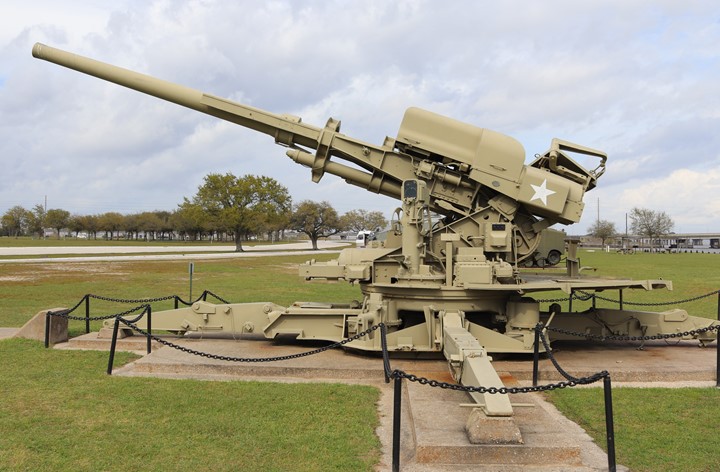
The Fisher Body produced 120mm M1
Anti-Aircraft gun. Author's photo.
155mm "Long Tom"
Gun parts: Flint Fisher Body #1
made parts for this weapon.

A 155mm "Long Tom" gun. Author's
photo.
B-29 Jigs and Fixtures: Flint
Fisher Body #1 built jigs and fixtures that were used for assembling the
wings, wing flaps, stabilizers and nacelles. These fixtures were
then sent to Fisher Body plants in Lansing, MI, Cleveland #1, OH,
Cleveland #2, OH, Fleetwood in Detroit, MI, Pontiac, MI, Memphis, TN, and
Grand Rapids, MI.
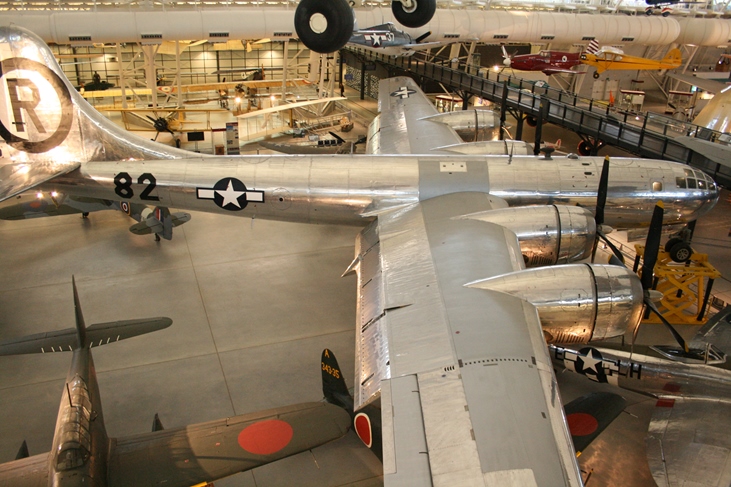
Flint #1 fixtures were instrumental in
building the wings, wing flaps, stabilizers and nacelles. This is
B-29 Enola Gay, which had many Fisher Body components in it.
Author's photo.
B-25 Jigs and Fixtures: As early
as December 31. 1941 Flint Fisher Body #1 was making jigs and fixtures
for B-25 components being assembled by the Fisher Body Plant in
Memphis, TN. These components included wing sections, rudders, and
vertical and horizontal stabilizers.
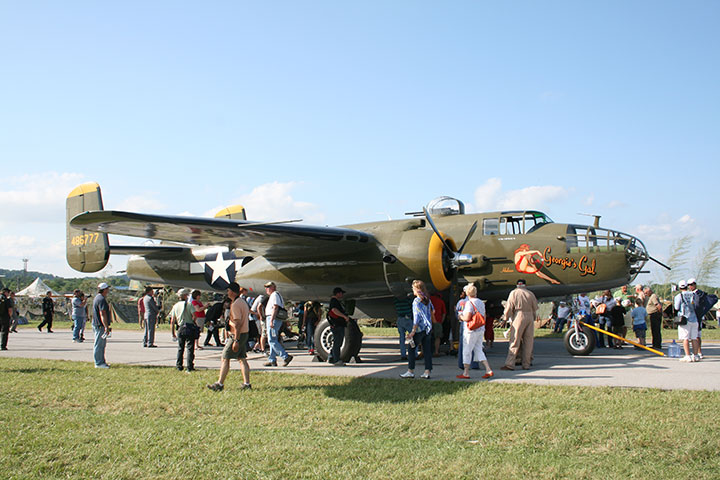
Components from the Memphis Fisher Body
Plant went into making B-25s at Fairfax, KS. This is a Fairfax
built B-25. Author's photo.
XP-75 Aircraft Jigs and Fixtures:
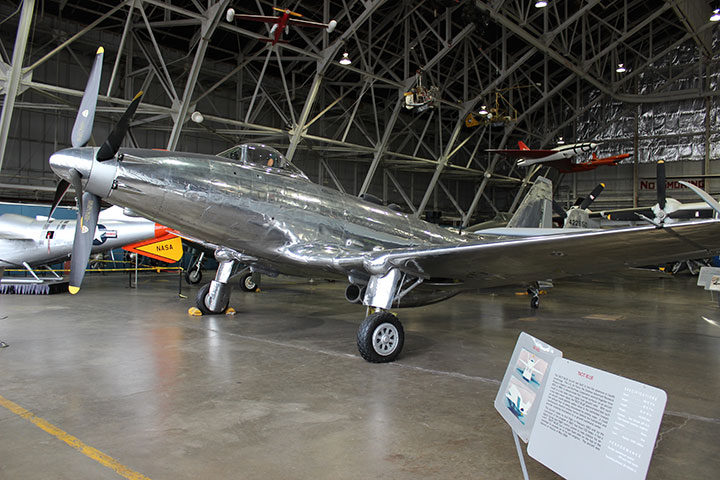
The Fisher XP-75. Only 7 were built,
and the lone survivor is located at the Museum of the United States Air
Force in Dayton, OH. Author's photo.
|